マニュアル作成のポイント④「確認」を処理作業化
倉庫現場は個別色が強いため、改善例を挙げ始めるときりがありません。そのため、ここではどの倉庫にも当てはまる共通項を7つ挙げ、解説したいと思います。今回は、マニュアル作成のポイント④として、「確認作業の処理作業化」について取上げます。
倉庫管理マニュアル「7つのポイント」
ポイント①:作業環境を整備する
ポイント②:入荷管理を徹底する
ポイント③:ロケーション表示を簡略化する
ポイント④:確認作業を処理作業化する ← 今回はコレ!
ポイント⑤:注意力を喚起する工夫を随所に盛り込む
ポイント⑥:バーコードを活用し、リアルタイムで正確な在庫管理を行う
ポイント⑦:バーコード管理の環境を整える
● ダブルチェックは機能しない
ヒューマンエラーを減らす対策として、よく行われるのがダブルチェックです。〝一度確認するだけでは見逃すかもしれないけれど、二度ないし複数のチェックをかければミスを軽減できる〟、私の経験上、このダブルチェックは誤出荷防止にあまり役立ちませんでした。
最大の理由は〝過信〟です。
作業者自身がダブルチェックをする際、自分が一度「大丈夫」と思った確認を、自らもう一度行うことになります。すでに「問題なし」と判断しているわけですから、二度目以降は「合っている」という前提のもとに目を通してしまいます。
人間の目は不思議なもので、「合っている」と思い込みながらチェックした場合、仮に明らかな間違いがあっても目に入りません。見ているのに、見ていないのです。そうやってミスはダブルチェックをすり抜けていきます。
では、複数人でのダブルチェックはどうでしょう。この場合も人間の心理として難しい上に、コストがかかります。作業者自身のダブルチェックと同様、「一人目が確認しているので大丈夫」という前提のもとで、二人目の確認作業が行われるからです。どうしてもチェックの目が緩くなってしまうのです。しかも確認する人の数が増えるほど人件費は増加します。
ダブルチェックが機能しない理由はほかにもあります。誤出荷事故の発生件数自体が作業量に比べて非常に少ないということです。
仮に10件や20件に一度といった確率で誤出荷事故が頻繁に起きている場合、ダブルチェックの担当者は〝見つけがい〟があるのでチェックの目が厳しくなるかもしれません。
しかし、よほど管理がずさんな倉庫でない限り、日々のチェックでミスはほとんど見つかりません。すると人間は、どうしてもチェック自体が疎かになってしまうのです。
例えば、タバコを吸う人が年に一度か二度、タバコを反対にくわえてしまうことがあるとします。その年に数回のミスのために日々、「タバコの向きよし!」と確認できるでしょうか。少なくとも私には無理です。極端に言えば、ダブルチェックとはそういう心理的な無理難題を作業者に与えているようなものなのです。
● 作業者の注意力が問題ではない
「作業者が注意を怠ったからミスが生じたのだ」ともよく言われます。しかし事故の原因を作業者の不注意のせいにしても問題は解決しません。
ピッキング作業の際、商品現物表示の品番とピッキングリストにある品番を突き合わせて確認したとき、合っていると思い込んでミスが生じることがあります。確かに注意力不足が原因かもしれませんが、厳密に言えば、合っていると思い込んで〝確認作業が抜け落ちてしまう〟ことでミスが起きています。
では、なぜ確認作業が抜けてしまうのでしょうか。ダブルチェックの項目でもお伝えしたように、人間は自分が確信を持っていることについては逐一、注意力を保つのは難しく、見落としてしまうものなのです。
「誤出荷の原因は注意力不足です」「確認不足だったので、次回はもっと注意して作業します」そのような事後報告書は、当社ではあり得ません。
「なぜヒューマンエラーが起きたのか」を徹底究明し、「どうすればそのミスを防ぐことができるのか」という改善策を具体的に考え出し、一対一で指導を徹底できるまで、何度でも事後報告書をやり直させます。注意力不足や確認不足を誤出荷の原因にしている限りは、ミスはなくならないと心得てください。
誤出荷を高い精度で食い止める「3つの勘所」とは?
● ミスを食い止める〝勘所〟を設けることが大事
では、何が必要なのかと言えば、〝注意して確認しなくても誤出荷を減らせる仕組み〟を作り込むことです。そのために重要となるのが、発生したミスを食い止める〝勘所〟です。人間が何度チェックしてもヒューマンエラーは起こり得るわけですから、仮にミスが生じても仕組みで止めてしまえばいいのです。
●「ロケ行って品番」で〝自然ダブルチェック〟を働かせる
ダブルチェックという意味でいうと、「ロケーション」「品番」「数量」の三つのうち、「ロケーション」と「品番」の二つが特に重要です。「ロケ行って品番」によってダブルチェックが〝自然〟にかかるからです。
在庫管理のシステム上、ピッキングリストに割り振られているロケーション番号の棚に行けば、間違いなくその品番の商品が入っています。しかもフリーロケーションの場合、隣の棚にはまったく異なる品番の商品が入っていますから万が一「A─02」を「A─03」と読み間違えて隣の棚に行ってしまっても、品番がまったく異なるので気づくことができるのです。
仮に、本来の「A─02」ではなく、隣の「A─03」の棚に間違って行ってしまい、品番を確認したところ、本来の「6312」ではなく「6321」の品番の商品が入っていたとしましょう。この場合は、「誤ピッキングをしても仕方がない」と考えています。「6312」と「6321」は酷似しているため、注意力が不足していれば間違える可能性は十分に考えられるからです。
よく似た品番在庫が隣接しているとミスにつながりやすいのは倉庫管理のよくある話です。しかし、フリーロケーションの場合、隣の棚にここまで似通った品番の商品が入る確率はかなり低いといえるでしょう。本来の品番が「6312」であれば、隣の棚には「4598」といった明らかに異なる品番在庫が入っているからです。
つまり「ロケ行って品番」を仕組み化することで、目的の商品を効率的に探せるだけでなく、ピッキングミスが起こり得ない環境にできるのです。作業員が意識しないところで〝自然ダブルチェック〟を働かせているということです。
事実、当社が管理する物流倉庫では「ロケ行って品番」を〝憲法〟として現場に浸透させ、当社独自のシステム管理を掛け合わせることで高い物流品質を達成し続けています。
それでもミスが生じる可能性をゼロにできない原因は、作業者の独自の判断でロケーションに行かずにピッキングしてしまうこと。ヒューマンエラーが起きるリスクを考慮し、現場を教育し続けるしか、誤出荷ゼロを達成する方法はありません。
●区別しやすい品番を割り振る
荷主企業様にかかわることですが、品番の付け方も重要です。特にミスを誘発しやすいのは、長い文字列の一部を変えただけのような品番です。
例えば「JLO─00210005」「JLO─00310005」「JLO─00410005」といったように、中の数字1文字だけを変えた表記の場合。これは「読み間違いをしてください」と作業員に言っているようなものです。また「JLO─00210005r」「JLO─00210005l」といったように、文字列の最後にアルファベットが付記されている品番もよく見かけます。これも見間違えるリスクを高めます。
ミスを起こさない品番の付け方で望ましいのは、〝区別しやすい品番を割り振る〟ことです。数字やアルファベットが統一されていなければ品番の区別はつきやすく、見間違いを防げます。
小さなことかもしれませんが、こうした泥臭い対策を積み上げていくことで誤出荷をゼロに近づけることができるのです。
● 確認作業を処理作業化する
人間は注意力を維持した〝確認作業〟が苦手です。ですから「確認作業」を「処理作業化」してしまえば、〝自然ダブルチェック〟を働かせることができます。
確認作業を処理作業化するとは、一体どういうことでしょうか。「確認作業」というのは、「1234」が「1234」であることを確認しながら進める作業のことです。
一方の「処理作業」というのは、「1234」が「1234」であることを逐一確認する必要はなく、バーコードスキャンで処理できる作業のことです。一つひとつの確認が不要なので余計なことを考えずに作業ができますし、万が一「1243」の商品が混ざっていても誤出荷事故を未然に防止することができるのです。
● 検品時の事故をゼロにする仕組み
では、処理作業の具体例を挙げましょう。当社の物流倉庫の場合、検品時の作業を処理作業化することで、誤出荷を限りなくゼロに抑えてきました。
具体的には「商品に同梱する納品書」「お客様が購入した商品」「運送会社の荷札」の三つのバーコードをスキャンし、すべて正しく揃った状態で「検品OK」となる仕組みです。
まず、納品書のバーコードをスキャンし、お客様が購入した商品情報のリストを検品システムの画面上に呼び出します(図表)。
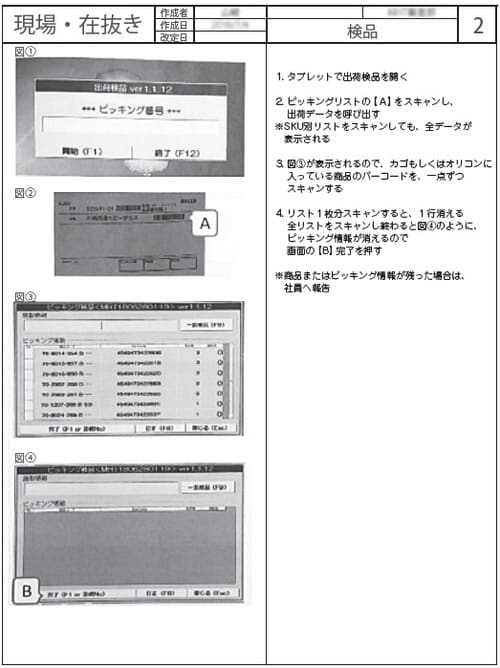
2.ピッキングリストの【A】をスキャンし、出荷データを呼び出す
※SKU別リストをスキャンしても、全データが表示される
3. 図③が表示されるので、カゴもしくはオリコンに入っている商品のバーコードを、一点ずつスキャンする
4.リスト1枚分スキャンすると、1行消える全リストをスキャンし終わると図④のように、ピッキング情報が消えるので画面の【B】完了を押す
※商品またはピッキング情報が残った場合は、社員へ報告
次に商品のバーコードを一つずつスキャンし、検品システムに表示されている商品情報のリストを消し込んでいきます。すべての消し込み処理が終わると、最後に荷札のバーコードを読み取り、完了ボタンを押して検品終了です。
以上の検品工程には、例えば数字を突き合わせるといった確認作業はありません。バーコードを読み取るというシンプルな処理作業だけで終わるので、思い込みやうっかりミスなどのヒューマンエラーが入り込む隙がないのです。
仮に、検品作業のどこかのタイミングでミスが生じても、間違いを示すブザーが鳴るようにしているため、見逃すことはありません。誤ピッキングしているなど、前工程でミスをしていた際も同様です。本来の商品とは異なる商品のバーコードをスキャンすると、消し込み処理は行えませんから、ピッキングミスが抑止できます。
万が一、検品終了後に商品または商品情報が残った際は、現場責任者に報告し、問題解決に当たります。「納品書→商品情報→荷札」この三つの〝勘所〟を設けることで、誤出荷を高い精度で食い止められるのです。
● 1件の注文ごとにカゴを分けて管理する
以上の検品工程で誤出荷はほぼ完璧に防ぐことができますが、それでもヒューマンエラーは起こり得ます。例えば2件の注文情報を混在してスキャンすると、誤出荷につながるリスクが起こります。
したがって、検品作業は1件ずつ注文ごとに分けて行うよう徹底しています。具体的には、ピッキング作業時から1件の注文ごとに個別のカゴで商品を管理し、複数の注文品が混在しないように工夫するなどです。
〝これを守れば絶対に誤出荷しない〟という作業の勘所を設け、それをルール化して現場に徹底させる。この〝勘所〟の設定と運用こそ、誤出荷事故をゼロにする最大のポイントなのです。
山田 孝治
株式会社三協代表取締役社長