「都度生産方式」で究極の効率化を実現
日本企業の中で今も企業価値やビジネスモデルをグローバルに維持している企業は極めて少ないが、その代表がトヨタであることに誰も異論はないだろう。
なぜトヨタはその地位を保ち続けているのか? 簡単に言えば、造れるだけ造るプロダクトアウトの生産方式を、マーケットインの「都度生産方式」、つまり必要になった分だけ造る方式に変えるという自動車生産の革命を成し遂げたからだ。これによってトヨタは生産のプロセスに隠れていた膨大なムダをなくし、究極の効率化を実現した。そしてGMなど世界の巨人に勝っていった。これは世界の製造業の歴史に名を残す偉業だ。
トヨタがこの革命をスタートさせたとき、世界の自動車産業はまだ大量に造って市場に流すフォード型の大量生産モデル全盛の時代だった。トヨタはその発想を完全にひっくり返したのだ。それはモノ・ハードから、工夫・ソフトへの転換であり、まさに革命と呼ぶに値するものだった。
複雑な工程を極限まで合理化した「かんばん方式」
トヨタ生産方式でよく知られているのは、あらゆるムダを見つけ出し、なくす努力を続けるという基本理念や、必要なものを、必要なときに、必要なだけ調達し、造るという「ジャスト・イン・タイム方式」、そしてその核となる「かんばん方式」だ。
「かんばん方式」とは部品を入れた箱に「かんばん」と呼ばれる札をつけて、部品・製品の在庫管理をしたことに由来する。簡単に言うと、組み立ての現場は部品倉庫から箱単位で部品をとってきて組み立て、箱が空になったらまた部品倉庫にとりにいく。部品の現場は箱が減った分だけ部品を造る、あるいは協力メーカーから調達する。この箱の移動を「かんばん」の受け渡しで管理する。
いかにも現場ならではの素朴な管理方法だが、この単純明快な仕組みによって、数万点という部品からなる自動車という製品を売れた分だけ造り、膨大な部品を使った分だけ造る、補充するという、極めて複雑な工程を極限まで合理化することができたのだ。
それまでのフォード型生産は原料も部品もとにかく造れるだけ造り、加工し、組み立て、製品として市場に送り出すという方式をとっていたのだが、作業のスピードは工程によって違うため、現場のいたるところで材料・部品のだぶつきや不足が起きていた。
ヘンリー・フォードの時代はそれでも製品が圧倒的な競争力を持ち、造れば造るほど売れたから、そうしたおおざっぱなやり方でも莫大な収益を上げることができた。しかし、自動車メーカーの競争が激化し、市場ニーズも多様化して生産する車種も増えてくると、ロスをなくすことが大きな意味を持ち始めていた。
かんばん方式は、生産のジャスト・イン・タイム化を推進した大野耐一が、アメリカのスーパーマーケットの話を聞いたときに思いついたという。大野は、必要なものを色々な売り場から必要な分だけ必要なときにとってくることができるスーパーマーケットの売り場を生産の前工程、お客を後工程に置き換えれば、こうしたロスを減らすことができると考えたのだ。経営陣が現場をよく知っていて、「何が問題か」「どうすればよくなるか」を常に考えているところにトヨタの強さがある。
常に生じるあらゆるムダを徹底的になくす努力、その一環としての「カイゼン」もトヨタの成功によって日本のあらゆる産業に広がった。
[図表]フォード型大量生産と、トヨタかんばん方式の違い
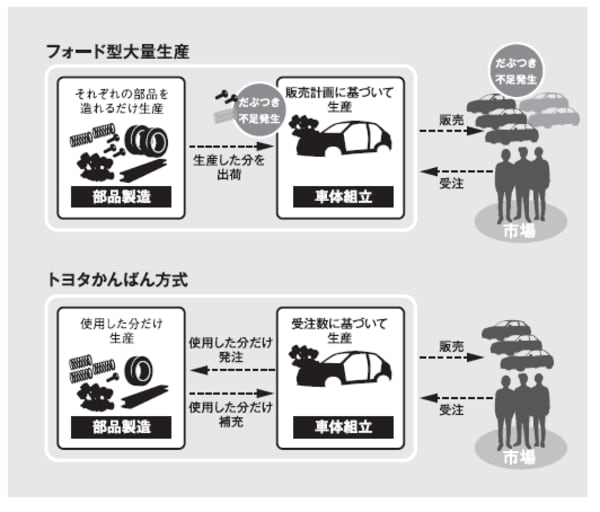